In general, laboratory mock-up methods were used to simulate nail installation in the field. Figure 3 depicts the general configuration considered by the test program, which includes a wood stud, exterior sheathing, and the fiber-cement panel. Nails were installed in the center of the specimens in the proud, flush, or recessed condition (Figure 4). A 15-degree coil siding nailer was used for pneumatic installation of the nails. Pneumatic nailing is a common installation approach due to its efficiency compared to hand nailing. The specific pneumatic nailer used for specimen fabicration was selected due to its representation of common commercial pneumatic nailers, availablity to the authors, and compatiblity with the coil siding nails selected for the test program. The test program also considered the interface between the exterior sheathing and the fiber-cement panel. When sheet-type weather barriers, such as those fabricated from spun-bonded olefin fibers, are included in the wall assembly, installers often use cap nails to mechanically fasten the sheet to the exterior sheathing. The cap nails create a gap between the exterior sheathing and the back surface of fiber-cement panels, which, according to hypothesis, influences the size of the spall on the inboard face of the fiber-cement board created during nail installation (Figure 5).
The test program considered five cases that incorporated variations in the nail head condition and substrate configuration (i.e. the gap between the substrate and the fiber-cement panel). Items 1 through 3 describe the five test cases in detail. Gypsum Cornice Machine

Specimens were pre-drilled at the nail locations, and nails were then installed proud within the holes by hand. This case was used as a control.
Specimens were not pre-drilled and were placed directly against the exterior sheathing of a mock-up frame simulating a typical wood-framed, gypsum-panel-sheathed stud wall and fastened using the pneumatic nailer adjusted such that the nail heads were proud.
Specimens were not pre-drilled and were placed against cap nails used for the mechanical attachment of a sheet-type weather barrier installed over the exterior sheathing of a mock-up frame to simulate a typical wood-framed, gypsum-panel-sheathed stud wall. The cap nails created an approximately 3.2 mm (0.13 in.) gap between the sheathing and the fiber-cement specimen. Nails were then installed using the pneumatic nailer, adjusted such that the nail heads were:
• Recessed by approximately 0.51 mm (0.02 in.) (case 3.c).
Each strength test was performed by inserting the test specimen into a test machine with the nail pointing up through a 76-mm (3-in.) diameter round hole in a steel plate used as a restraint. The circumference of this opening provided support to the specimen during the test. A drill chuck was used to grip the shaft of the nail, and a load was applied by the test machine via self-aligning linkages. The load was continuously applied at a constant displacement rate and monitored by a 113-kg (250-lb) capacity load cell. Crosshead displacement was electronically monitored with a linear variable differential transformer (LVDT). A data acquisition system interfaced with a personal computer digitally recorded the data. The failure mode and maximum load at which the nail head pulled through the specimen was recorded for each test. Figure 6 is a schematic sketch of the test setup.
For each product, six specimens were tested for each of the five test cases, for a total of 30 tests per product.
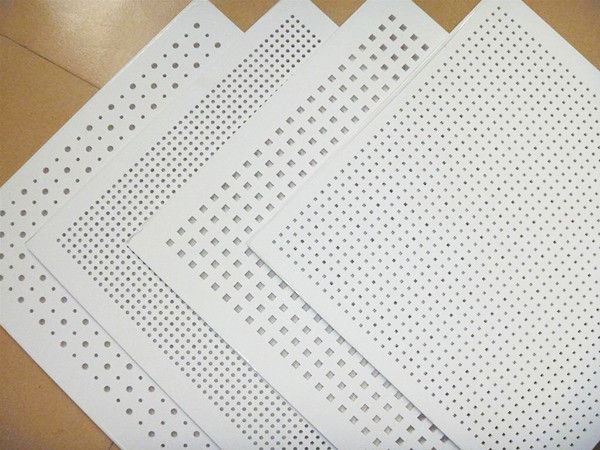
Mgo Board Equipemnt Factories Your email address will not be published. Required fields are marked *