Autonomous mobile robots (AMRs) can streamline material handling in manufacturing, logistics, warehousing, and more, yet many facilities still primarily rely on conveyor systems. To serve as a flexible bridge between fixed conveyors and production lines, Interroll designed a light conveyor platform (LCP) to facilitate the handling of lightweight goods with AMRs from Mobile Industrial Robots (MiR).
Interroll’s innovative LCP integrates with AMRs from MiR, enhancing efficiency and safety in material handling. Image: MiR Incline Conveyor
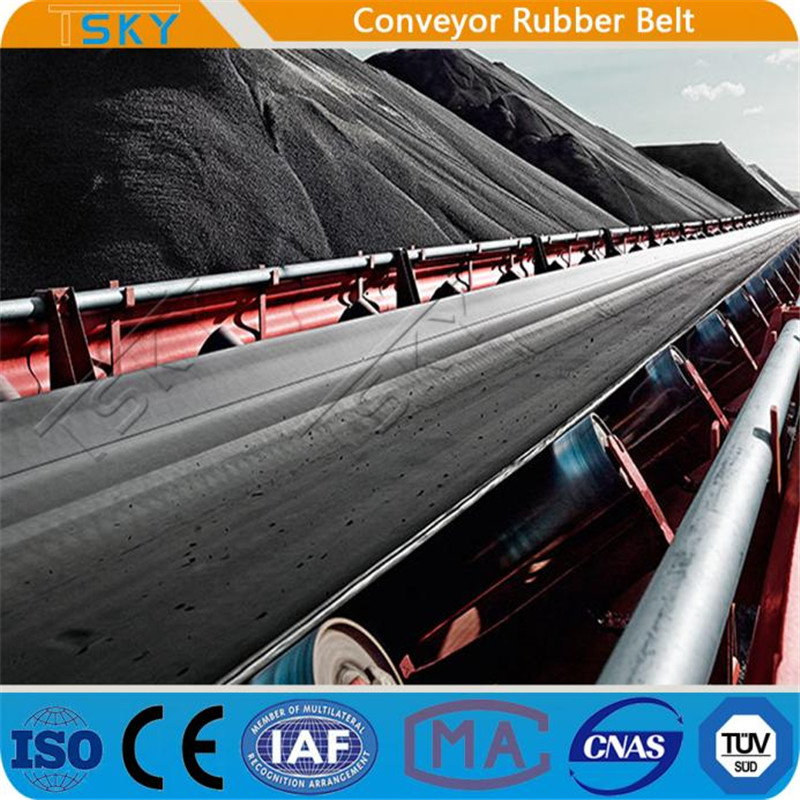
MiR’s AMRs are versatile robot platforms that accommodate top modules and other accessories to enhance their functionality. Interroll’s LCP AMR top module is the newest certified application in the MIR Go partner program, the largest ecosystem of AMR applications with more than 160 top modules that seamlessly connect to the mobile robots.
As part of its rigorous testing process, Interroll implemented the new LCP AMR top module with a MiR250 robot in its Center of Excellence in Sant Antonino, Switzerland. Specializing in the production of techno-polymer injection-molded parts, the facility spans two floors, presenting a unique logistical challenge. Previously, material handling from production to the logistics area required manual labor because no other logistics solution could offer the flexibility required for multi-floor operations. MiR’s AMRs effortlessly navigate this multi-floor environment, autonomously using elevators to move between floors.
The MiR250 with Interroll’s light conveyor platform top module moves autonomously between floors using elevators. Image: MiR
To further optimize processes, Interroll utilizes MiR Insights, MiR’s cloud-based software that visualizes key performance indicators, such as distance driven, completed missions, and robot utilization rates. This software provides insights into high-traffic areas, enabling Interroll to enhance robot workflows and throughput. Since the introduction of MiR Insights in June 2023, the MiR250 operates an average of 22.3 hours per day, covering 65 mi (106 km) within the factory premises.
The combination of the MiR250 with the LCP AMR top module has significantly reduced manual handling and transportation times, allowing Interroll’s skilled workforce to focus on tasks requiring human expertise, creativity, and decision-making. The company anticipates a positive ROI due to increased efficiency and reduced labor costs.
Rachael Pasini has a master’s degree in civil and environmental engineering and a bachelor’s degree in industrial and systems engineering from The Ohio State University. She has over 15 years of experience as a technical writer and taught college math and physics. As a Senior Editor of Design World and Fluid Power World, she covers hydraulics, pneumatics, linear motion, motion control, additive manufacturing, robotics, warehouse automation, and more.
Browse the most current issue of Design World and back issues in an easy to use high quality format. Clip, share and download with the leading design engineering magazine today.
Top global problem solving EE forum covering Microcontrollers, DSP, Networking, Analog and Digital Design, RF, Power Electronics, PCB Routing and much more
The Engineering Exchange is a global educational networking community for engineers. Connect, share, and learn today »

Conveyor Scraper Copyright © 2024 WTWH Media LLC. All Rights Reserved. The material on this site may not be reproduced, distributed, transmitted, cached or otherwise used, except with the prior written permission of WTWH Media Privacy Policy | Advertising | About Us